Introduction to cold working process of quartz glass
Click:
-Time:2019-08-06 10:43
Introduction to cold working process of quartz glass
The deep processing of quartz glass refers to the processing of quartz glass raw materials (tubular, rod-shaped, sheet-like, block-shaped) into quartz devices required by users, and is divided into two types of cold working and hot working in the adding method. The following is a detailed description of the cold working using glass.
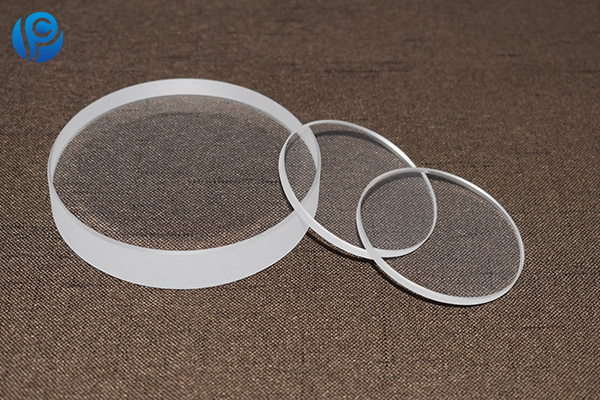
Cold processing mainly includes cutting, grinding and polishing:
1. Cutting: The quartz tube or quartz glass plate is mainly cut by a diamond saw blade or a diamond saw blade. Multi-knife cutting machine, wire cutting machine, mainly used for quartz crucible and quartz block cutting. Laser cutting machine, internal circular cutting machine, mainly used for cutting guide plates.
2. grinding: flat grinding disc, single-axis, double-axis polishing machine, coarse grinding: Hcp in 10~20μm smoothness ▽ 2. Plane milling machine, multi-function milling machine, fine grinding: Hcp in 6.3μm finish ▽ 6. Drilling machine, lathe, Inner garden, outer garden grinder, rough grinding: Hcp is below 6μm▽7.
3. Polishing: Multi-axis polishing machine: Hcp < λ, that is, 0.5 μm or less. 1 The purpose of rough grinding is to shape the workpiece to a certain geometry. After processing the surface of the quartz glass with a particulate abrasive or a combination of abrasives, the surface irregularity Hcp is 10 to 20 μm, and the coarse grinding is performed by hand grinding on the grinding disc with a loose abrasive or mechanical grinding with a combined abrasive. The bulk abrasives are green SiC (corundum) and fused white corundum; etc.; 60#~12# fused corundum sand can be used to achieve ▽2. The combined abrasive has SiC resin and diamond grinding wheel. Rough grinding is preferably carried out with a bonded abrasive on a surface grinder or milling machine. 2. Fine grinding: The purpose is to improve the roughness of the surface, to obtain the near-finished geometry of the workpiece, to lay the foundation for polishing, and to grind the surface with the bulk abrasive, the unevenness Hcp<6.3μm; the dimensional accuracy is 0.5~1.0mm. There are also two types of fine grinding: manual bulk material + flat grinding disc. Generally, a small grinding disc is used, the linear speed is above 12m/s, and the workpiece is elliptical in the grinding disc, and the normal rotation is 180°. Mechanical grinding, upper plate, machining parts are fixed on a circular cast iron plane. Single-axis polishing machine, double-axis bubble foot (H015 type) shaft polishing machine. 3. Fine grinding: The purpose is to further improve the quality of the glass surface, minimize the thickness of the damaged layer that must be completely removed by polishing, and further correct the geometric size. Hcp <6 μm, ▽7 or so. The main indicator of fine grinding is the finish. The inspection method is observed with the naked eye under reflected light. The fine grinding abrasive is 120~14μm. Should avoid scratches as much as possible. 4. Polishing Hcp < λ; that is, <0.5 μm. The purpose of polishing is that the microscopic fluctuation of the glass feldspar is smaller than the wavelength of the light wave. The polished stone can be polished; the glass is well permeable to light. Polishing glue for asphalt + rosin gas; the polishing workshop requires constant temperature. There are two kinds of polishing equipments, high speed and low speed. Various tool holders.
If you are interested in the quartz glass plate or need to consult, please click on our online customer service, or call us.
Pan Chao, customized different quality specifications of the glass.
Pan Chao special industrial glass, tailored for your different quality of the glass.
Welcome sending your inquiry: Phone : +86 13569413718 Email: info@panchaoglass.com
If you are interested in the quartz glass plate or need to consult, please click on our online customer service, or call us.
Pan Chao, customized different quality specifications of the glass.
Pan Chao special industrial glass, tailored for your different quality of the glass.
Welcome sending your inquiry: Phone : +86 13569413718 Email: info@panchaoglass.com
Related articles
- Classification of Heat Resistant Glass for Instruments
- Physical and chemical changes of heat resistant glass during
- Classification and Properties of Heat Resistant Glass Sheets
- high transmittance small diameter quartz glass tube
Recommend
- Introduction to Borosilicate Glass
- High Temperature Resistant Glass: protecting world under extr
- High Temperature Resistant Glass: protecting world under extr
- High Temperature Resistant Glass: protecting world under extr
- What is optical glass
- Development history of aluminum silicon glass
- The best transparent polymer glass
- Classification of glass tube mirrors
- What is a mirror glass
- What is high-temperature glass
Rank
- Application of high temperature resistant glass
- Precautions in the process of quartz tube cutting and picklin
- Introduction to Borosilicate Glass
- The difference between high borosilicate glass, medium borosi
- High Temperature Resistant Glass: protecting world under extr
- High Temperature Resistant Glass: protecting world under extr
- High Temperature Resistant Glass: protecting world under extr
- What Glass Has the Highest Temperature Resistance
- What are the advantages and disadvantages of quartz tube heat
- Comparison Between LOW-E Glass and Ordinary Insulating Glass
Latest articles
- Introduction to Borosilicate Glass
- High Temperature Resistant Glass: protecting world under extr
- High Temperature Resistant Glass: protecting world under extr
- High Temperature Resistant Glass: protecting world under extr
- What is optical glass
- Development history of aluminum silicon glass
- The best transparent polymer glass
- Classification of glass tube mirrors
- What is a mirror glass
- What is high-temperature glass